Top 10 Manufacturing Quality Issues Reported in 2024 & How to Avoid Them in 2025
- swichansky2
- Dec 16, 2024
- 4 min read
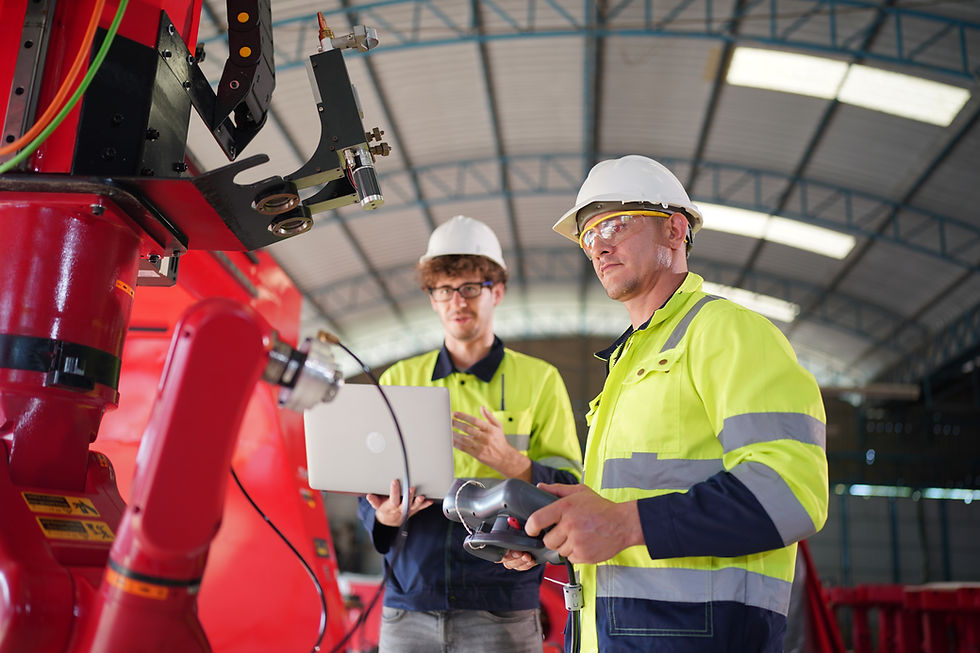
As we enter 2025, manufacturers face an increasingly complex landscape of challenges that impact product quality. From supply chain disruptions to the integration of emerging technologies, maintaining high-quality standards is more demanding than ever. In 2024, we saw several recurring quality issues that continue to affect manufacturers globally. Below, we explore the top 10 quality issues reported in 2024 and offer actionable solutions to help businesses avoid these challenges in the year ahead.
1. Inconsistent Product Quality Due to Automation Failures
The Issue: Automation has revolutionized manufacturing, but many businesses are grappling with inconsistent product quality caused by poorly calibrated systems, outdated programming, or lack of human oversight.
How to Avoid in 2025:
Integrate AI-driven quality control systems that can detect defects in real-time, ensuring a higher degree of precision.
Maintain a balance by combining human expertise with automated processes, especially in critical inspections and quality checks.
2. Material Shortages and Substitution Risks
The Issue: Global supply chain disruptions have led to material shortages, forcing manufacturers to rely on alternative, sometimes lower-quality materials. This can result in reduced product quality or performance.
How to Avoid in 2025:
Strengthen supplier relationships and diversify your network to reduce reliance on single sources.
Perform rigorous testing on any substitute materials to ensure they meet your product’s specifications and performance standards.
3. Incompatibility Between Legacy Systems and New Technologies
The Issue: As manufacturers move toward smart factories and Industry 4.0 solutions, integrating legacy systems with newer technologies remains a challenge, leading to inefficiencies and potential quality issues.
How to Avoid in 2025:
Adopt IoT platforms that can integrate legacy systems with newer technologies for seamless data flow.
Regularly upgrade equipment and systems to avoid operational silos and maintain compatibility with modern solutions.
4. Cybersecurity Vulnerabilities
The Issue: With increased connectivity, the risk of cyberattacks targeting production systems and compromising quality data is a growing concern.
How to Avoid in 2025:
Implement robust cybersecurity measures such as ISO/IEC 27001 frameworks and encryption protocols to safeguard data integrity.
Perform regular system updates to ensure your software and devices are protected against the latest vulnerabilities.
5. Human Error in Hybrid Work Environments
The Issue: Despite automation, human workers are still essential in many aspects of manufacturing. However, a lack of training and insufficient understanding of advanced technologies often lead to errors in quality control.
How to Avoid in 2025:
Invest in continuous training programs to upskill workers on new systems and best practices.
Utilize augmented reality (AR) or wearable tech to provide real-time guidance during production processes, minimizing human error.
6. Pressure to Meet Customization Demands
The Issue: With consumer demands for personalized products growing, manufacturers are under pressure to deliver customized products quickly. However, these increased complexities can sometimes compromise quality.
How to Avoid in 2025:
Invest in modular manufacturing systems that can efficiently handle custom orders without sacrificing quality.
Use digital twins to simulate and test customized products before physical production, reducing errors and rework.
7. Regulatory Compliance and Sustainability Challenges
The Issue: As environmental concerns and regulations tighten globally, manufacturers must navigate the complexities of sustainability while ensuring compliance with varying standards—without compromising quality.
How to Avoid in 2025:
Collaborate with sustainability experts to ensure your processes meet eco-friendly standards while maintaining product durability.
Adopt compliance management software that automatically tracks changes in regulatory requirements across regions.
8. Equipment Wear and Tear Impacting Precision
The Issue: Advanced machinery used in manufacturing is prone to wear and tear, leading to precision loss, increased downtime, and inconsistent product quality.
How to Avoid in 2025:
Implement predictive maintenance tools that monitor equipment health and schedule repairs before breakdowns occur.
Invest in high-quality components and ensure regular calibration to maintain machine performance.
9. Overwhelming Data and Lack of Actionable Insights
The Issue: Manufacturers are generating more data than ever from smart systems and IoT devices, but sifting through this data to extract valuable insights remains a challenge.
How to Avoid in 2025:
Leverage AI-driven analytics to analyze data in real-time and highlight key quality metrics.
Consolidate data into centralized dashboards, allowing teams to easily monitor performance and make data-driven decisions.
10. Quality Control Gaps in Global Supply Chains
The Issue: Manufacturers with global supply chains struggle to maintain consistent quality standards, especially with tier-2 and tier-3 suppliers who may not adhere to the same stringent controls.
How to Avoid in 2025:
Use blockchain technology to track and verify materials and components across the supply chain, ensuring transparency and consistency.
Conduct frequent audits and collaborate closely with suppliers to align quality standards globally.
Conclusion: Looking Ahead to a Quality-Driven 2025
In 2025, manufacturers will face even greater demands to balance efficiency with product quality. By addressing these key quality challenges head-on and leveraging new technologies, businesses can not only prevent quality issues but also set the stage for sustained success in an increasingly competitive marketplace.
By staying proactive and investing in solutions that integrate the latest advancements, manufacturers can ensure their processes remain efficient, their products high-quality, and their customers satisfied.
Call to Action: If you’re looking for ways to enhance your third-party quality containment processes in 2025, or need assistance navigating these challenges, reach out to our team. We’d love to discuss how we can support your quality initiatives and ensure continued success in the year ahead.