How to Address Manufacturing Quality Issues Effectively
- swichansky2
- Jun 7
- 4 min read
Updated: Jun 10
Manufacturing quality is a crucial aspect of any production process. Businesses strive to provide high-quality products that meet customer expectations. However, quality issues can arise at any stage of manufacturing. Addressing these issues effectively is essential to maintain customer satisfaction and protect the company's reputation. This post breaks down actionable steps you can take to tackle manufacturing quality issues head-on.
The Importance of Manufacturing Quality
Manufacturing quality goes beyond just meeting design specifications. It involves ensuring that products are durable, reliable, and safe for consumers. Poor quality can lead to increased costs, safety hazards, and damage to a company's reputation. For example, the recall of defective products in the automotive industry can cost millions and significantly impact customer trust.

Investing in good quality assurance practices not only saves money in the long run but also boosts brand loyalty. According to a study by the American Society for Quality, companies with better quality programs experience customer loyalty rates that are 25% higher than those without. Focusing on quality can create a competitive edge in the market.
Identifying the Root Causes of Quality Issues
The first step in addressing manufacturing quality issues is to identify their root causes. This involves analyzing processes, materials, and even human factors. Utilize methods such as the 5 Whys technique, where you keep asking "why" until you reach the fundamental issue.
Example of the 5 Whys Technique
Why is the product defective? It has a broken part.
Why is the part broken? It was not manufactured properly.
Why was it not manufactured properly? The machinery malfunctioned.
Why did the machinery malfunction? There was a lack of maintenance.
Why was maintenance lacking? The schedule was not followed.
Once you've identified the root cause, it's easier to implement effective solutions.
Implementing Quality Control Measures
Once the causes of quality issues are understood, implementing quality control measures is crucial. Here are some effective strategies to consider:
1. Establish Clear Standards
Create clear quality standards for every product. These should outline specifications, tolerances, and testing methods. When employees have clear guidelines, the likelihood of defects decreases.
2. Utilize Six Sigma Methodology
Six Sigma is a data-driven approach that focuses on improving quality by eliminating defects. By using statistical analysis, manufacturers can better understand variations in their processes and how to address them.
3. Regular Training
Invest in regular training sessions for your staff. A well-trained workforce can dramatically reduce errors and improve the quality of production. According to a study from the International Journal of Production Research, companies that invest in worker training see a 10% reduction in defects.

Involving Suppliers in Quality Assurance
Often, the quality of materials received from suppliers can influence the final product. Therefore, involving suppliers in quality assurance is essential. Establish clear expectations and involve suppliers in the quality control process by:
Setting quality benchmarks for them to meet.
Conducting regular audits to ensure compliance.
Investing in partnerships for joint improvement initiatives.
By collaborating with suppliers, you not only enhance the quality of your products but also strengthen your overall manufacturing process.
Implementing Continuous Improvement Practices
Quality should not be a one-time goal but rather a continuous objective throughout the manufacturing process. Here are actionable steps for fostering a quality culture:
1. Solicit Feedback
Encourage feedback from employees on the manufacturing processes and products. Employees often have valuable insights into how things can be improved.
2. Track Key Performance Indicators (KPIs)
Utilize metrics such as defect rates, production time, and customer returns to track performance. Regularly review these indicators to identify trends and areas for improvement.
3. Conduct Quality Audits
Implement routine internal audits to evaluate compliance with established quality standards. These audits should be thorough and involve all departments relevant to manufacturing.
Leveraging Technology for Quality Improvement
Modern technology offers numerous tools that can aid in improving manufacturing quality. Here are some ways to incorporate technology effectively:
1. Automation
Automating repetitive tasks minimizes the potential for human error, enhancing overall quality. For instance, using robotic arms can improve precision in assembly lines.
2. Quality Management Software
Invest in quality management software that can help streamline processes, store data, and generate reports. This software often comes with analytics tools that can aid in decision-making related to quality issues.
3. Real-time Monitoring
Utilizing IoT devices and sensors can provide real-time monitoring of production quality. This allows for immediate action if issues arise, preventing defective products from reaching consumers.
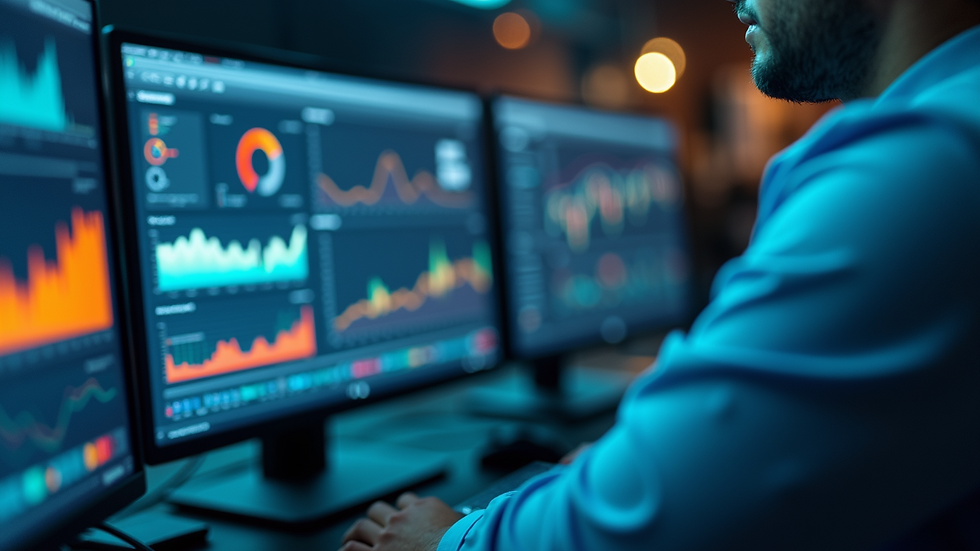
Fostering a Quality Culture in the Workplace
Creating a culture of quality within your organization is essential. Here’s how to do that:
1. Lead by Example
Management should demonstrate a commitment to quality through their actions. When leaders prioritize quality, it emphasizes its importance throughout the organization.
2. Reward Quality Initiative
Recognize and reward employees who contribute to quality improvement. This motivates individuals and teams to focus on quality and seek solutions proactively.
3. Open Communication
Encourage transparent communication regarding quality issues. Employees should feel comfortable reporting defects or suggesting improvements without fear of repercussions.
Addressing manufacturing quality issues effectively is not just about implementing new processes; it’s about fostering a culture where quality is a shared responsibility. By taking a structured approach to identifying, managing, and continuously improving quality, your company can secure its place as a leader in the manufacturing sector and achieve long-term success.
Manufacturing quality issues are inevitable, but with the right strategies in place, your company can tackle them efficiently. For more insights, you can visit prp quality. Stay committed to continuous improvement, and quality will become an integral part of your manufacturing process.